Definition of Tactile sensing
Tactile sensing relates to mapping contact pressures across a surface, often across complex surfaces like the hand, head, and other human body parts.
The more often-used terms "pressure" and "force" are related to "tactile," but both cannot capture the full complexity of contact mechanics. "Pressure" is a scalar value capturing solely magnitude and "force" is a vector expressing magnitude and direction.
Tactile measurement goes beyond by portraying the magnitude and distribution of contact pressures between two objects over an area as a matrix.
Pressure
Omnidirectional Scalar
Force
One Direction Vector
Tactile
Multi-DOF Surface
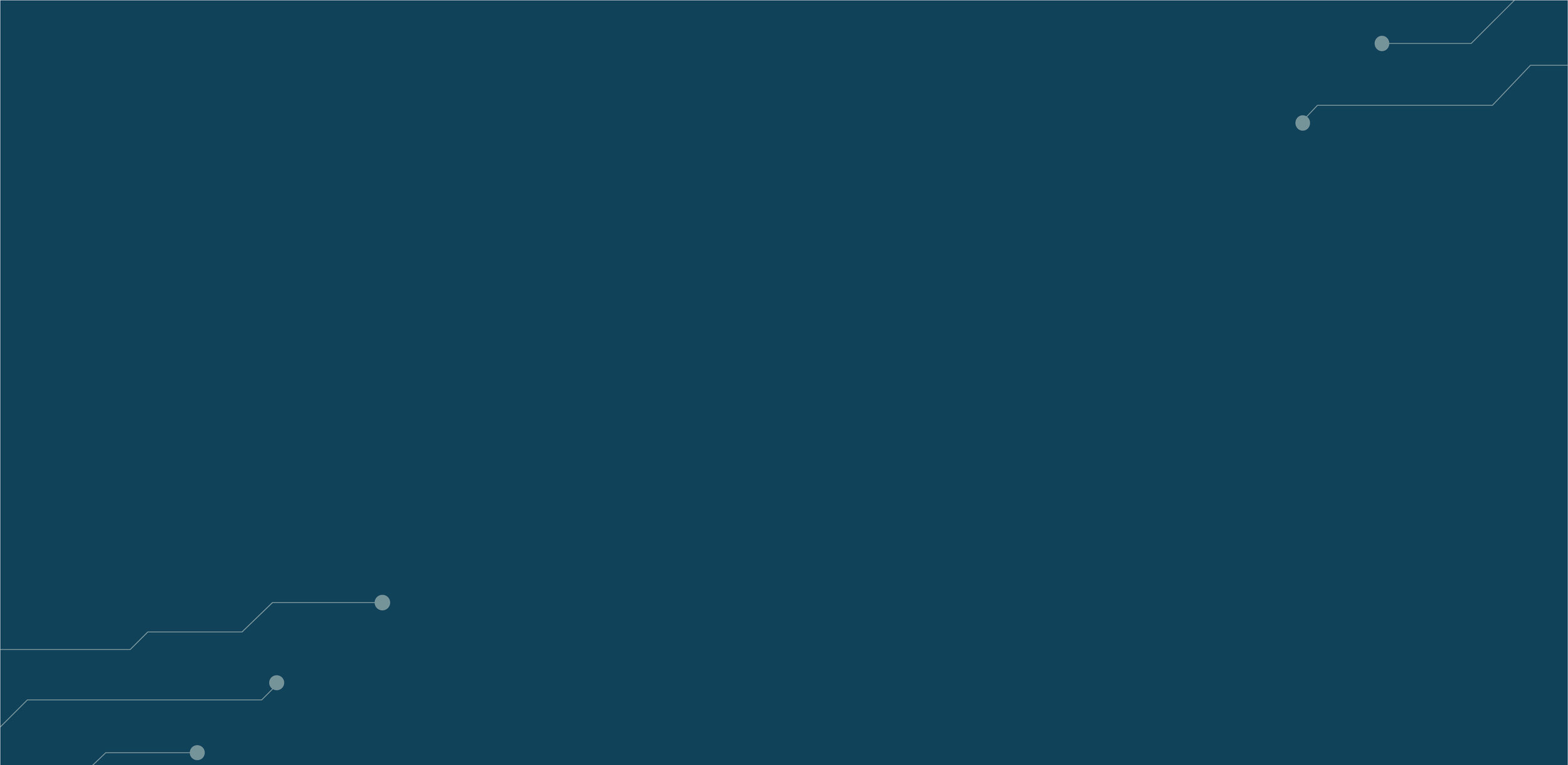
How does tactile sensing Work?
Tactile sensing is the technology of mapping and measuring the contact mechanics between two objects. Tactile sensing is closely related to pressure and force.
If you are searching for pressure measurement and mapping solutions, there are two main types of sensors: capacitance-based or resistance-based (piezoresistive sensors). Whereas resistive sensors work by measuring changes in the resistance of a semi-conductive materials, capacitive sensors work by measuring changes in the gap distance between two electrodes.
To function, the semi-conductive inks on a resistive sensor must go from a non-contacting state to a contacting state so the sensor performance is poor at low pressures. As the electrodes contact and rub against one another, the surface properties change on a microscopic level, which also changes the sensor behavior and thus requires frequent re-calibration or software compensation.
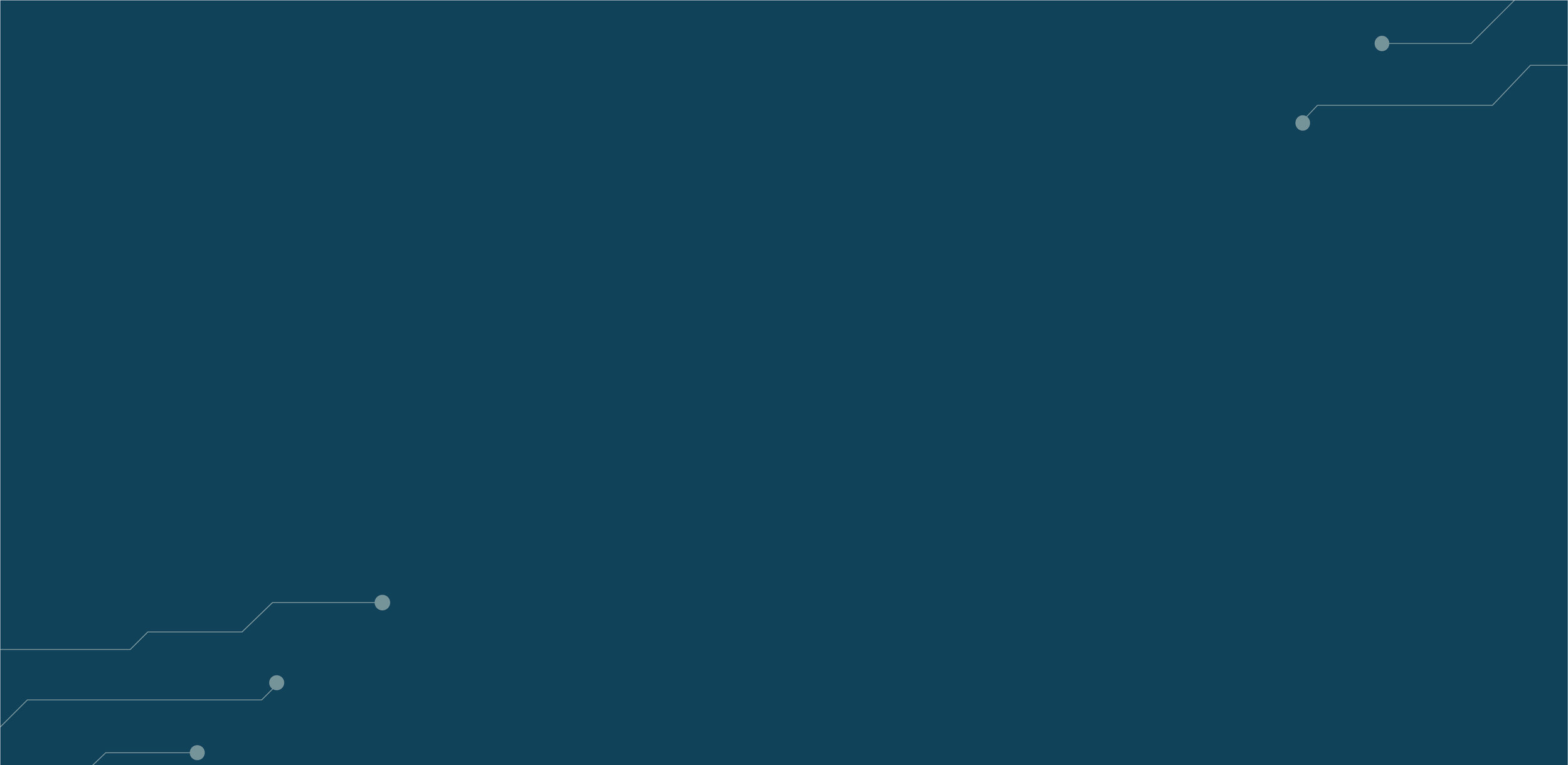
THE BENEFITS OF CAPACITIVE TACTILE SENSOR
The benefits of capacitive technology are that the two electrodes no physical interaction and operate in an elastic region, so the sensor is more sensitive and stable.
Another key benefit is that electrodes can be formed from any conductive material (conductive cloth, FPCB, metal fixtures) giving our sensors a wide range of design flexibility.
Capacitive tactile sensing has emerged as the preferred method for capturing contact-based pressure changes due to sensitivity, repeatability, stability and design flexibility.
A Comparison of tactile sensors
Capacitive Tactile Sensors | Resistive Tactile Sensors | |
---|---|---|
Construction | Conductive material separated by compressible dielectric |
Resistive ink printed on membrane |
Sensitivity | Excellent | Fair |
Repeatability | Excellent | Poor |
Number of Elements | Good | Excellent |
Design Flexibility | Excellent | Fair |
Speed | Fair | Excellent |
Temperature Stability | Excellent | Fair |
what is Capacitance?
Capacitance is a measure of an object’s ability to store electrical charge and has been demonstrated countless times through the classic physics class example of two electrodes with area A separated by an air gap D as shown. As the air gap decreases, the capacitance C increases.
We use this property to build sensor pads and arrays by separating the electrodes using a proprietary compressible dielectric matrix, which acts as a spring. Precision manufacturing techniques allow excellent repeatability and sensitivity, while advanced conductive materials allow for conformable, stretchable, industrial, and other hybrid sensor designs. The simplicity of the capacitive sensor design gives us a large degree of flexibility when creating custom sensor solutions.
Our Array Sensors
To build our Tactile Array Sensors, we arrange electrodes as orthogonal, overlapping strips separated by a proprietary compressible dielectric matrix, which acts as a spring. A distinct capacitor is formed at each point where the electrode strips overlap.
Precision manufacturing techniques allow excellent repeatability and sensitivity, while advanced conductive materials allow for conformable, stretchable, industrial, and other hybrid sensor designs.
By selectively scanning a single row and column, the capacitance, or local pressure, at that location is measured. Our proprietary drive and conditioning electronics can scan through an array at high speed while optimizing settings to achieve the maximum sensor response from each force sensing element.